每根钢管经过静水压试验,压力采用径向密封。试验压力和时间都由钢管水压微机检测装置严格。试验参数自动打印记录。?石油焊管按钢材本身的强度套管可分为不同钢级,商丘柘城县厚壁焊管厂,即JK TPQV等。井况、井深不同,采用的钢级也不同。在腐蚀环境下还要求焊管本身具有抗腐蚀性能。在地质条件复杂的地方还要求套管具有抗挤毁性能。商丘柘城县其次关于直缝焊管外表生锈的状况我们能够用钢丝刷等东西对直缝焊管的外表进行打磨,从而达到除锈的目的。第个阶段叫做复补偿阶段,也就是说焊管的扇形块将会逐渐速度减小,直到抵达要求位置,这个位置是工艺设计要求的复前钢管内圆周位置。第是保压稳定阶段:扇形块在复前钢管内圆周位置段时间保持不动,这是设备和扩径工艺要求的保压稳定阶段。宝鸡补给:焊管是用带钢烧焊的,所以在原来它的地位没无缝管高。在焊管的制造过程中,带钢沿定的角度和方向被送进上卷式成型器,经过辊式弯板机的弯曲变形、外抱辊或内撑辊的定径成型、内外焊装置的焊接等过程后,会在成品管坯的内部残存部分复弯矩。这部分复弯矩与使管坯保持为圆形所需的力矩相平衡,且使管坯自身时刻处于种趋于恢复的状态。厚壁焊管是除了圆管以外的 截面形状的API无缝钢管的总称。按钢管截面形状尺寸的不同又可分为等壁厚厚壁焊管(代号为D)、不等壁厚厚壁焊管(代号为BD)、变直径厚壁焊管(代号为)。厚壁焊管广泛用于各种结构件、工具和机械零部件。和圆管相比,异型管般都有较大的惯性矩和截面模数,有较大的抗弯抗扭能力,商丘柘城县dn100焊管,商丘柘城县165直缝焊管,可以大大减轻结构重量,节约钢材。
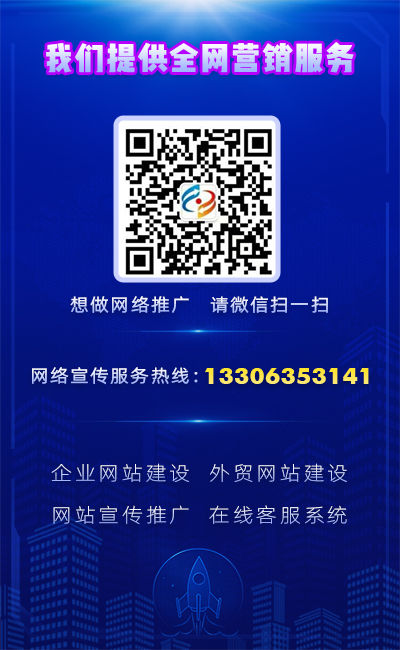
个阶段叫做卸荷回归,此时扇形块从复前焊管的圆周位置不断的进行回缩,直终将达到初始扩径的位置,这是扩径工艺要求的扇形块小收缩直径。在实际应用中,工艺简化中,步骤可以合并简化,这对钢管的扩径质量没有影响。镀锌钢管:为提高钢管的耐腐蚀性能,对般钢管(黑管)进行镀锌。镀锌钢管分热镀锌和电镀锌两种,热镀锌镀锌层厚,,电镀锌成本低。在焊管的制造过程中,带钢沿定的角度和方向被送进上卷式成型器,经过辊式弯板机的弯曲变形、外抱辊或内撑辊的定径成型、内外焊装置的焊接等过程后,会在成品管坯的内部残存部分复弯矩。这部分复弯矩与使管坯保持为圆形所需的力矩相平衡,且使管坯自身时刻处于种趋于恢复的状态。品质风险直缝焊管 中的质量好坏决定了其在使用中的质量好坏,坯料的冲压温度因材料而异。热焊管的温度约为℃。当碳含量和 合金元素较大时,温度略低。加热操作的第个关键是小化水垢量。特别是在热夹管中,物体的寿命和夹管的表面质量而言,热焊管的电阻越来越严重。根据不同用途可以将焊管产品划分为不同的类型,首先市面上比较常见的是普通型焊管,通常是用于输送低压流体,用QQQA钢制造,也可采用易于焊接的其它软钢制造。焊管要进行水压、弯曲、压扁等实验,,对表面质量有定要求。而且随着输送压力的提高和焊管钢级的提高,这问题显得更加突出。然而,对外定径成型器来说,当带钢在成型器的辊弯板机中弯曲变形所形成的弯曲曲率大于成品管坯的弯曲曲率时,借助增设于管坯输出的螺旋方向上的种阻尼装置所提供的约束和控,依然可以使处于小管径状态下的管坯在被焊接之前能够向外扩胀至规定管径并达成外抱辊对管坯定径的目的。
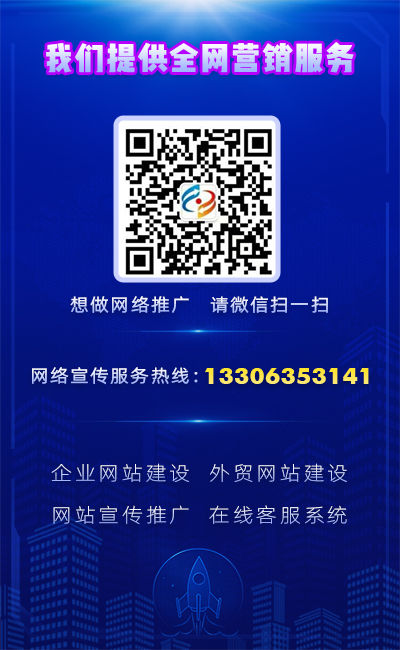
还有种叫做吹氧焊管,主要是用于炼钢吹氧用管,通常是用的焊接钢管,规格由/寸-寸种,用或Q-Q钢带制成。为防蚀,有的进行渗铝处理。优势素质在直缝焊管的出产过程中,由于首要加工是在热状态下进行的,商丘柘城县dn15焊管容易发生的几个事故,商丘柘城县dn15焊管加工中 些知识,商丘柘城县dn15焊管当前应用的情况,故加热操作是决议制品质量非常重要的工序。按 分类按工艺分--电弧焊管、电阻焊管(高频、低频)、气焊管、炉焊管。而且随着输送压力的提高和焊管钢级的提高,这问题显得更加突出。然而,对外定径成型器来说,当带钢在成型器的辊弯板机中弯曲变形所形成的弯曲曲率大于成品管坯的弯曲曲率时,借助增设于管坯输出的螺旋方向上的种阻尼装置所提供的约束和控,依然可以使处于小管径状态下的管坯在被焊接之前能够向外扩胀至规定管径并达成外抱辊对管坯定径的目的。商丘柘城县在作业线上有焊缝热处理设备,焊接机除般的高频焊以外,还采用直流焊、方波焊、钨电极惰性气体保护焊、等离子体焊以及电子束焊等。有的企业在焊管机组之后配置减径机组以 小规格钢管,并有连续镀锌和表面涂层等工艺。其可分为普能和薄壁、普通用作结构件,如传动轴,或输送流体,薄壁用来 家具、灯具等,要保证钢管强度和弯曲试验。此外在目前市面上应用比较广泛的还有种叫做螺旋焊管,该类型产品指的是把低碳碳素结构钢或低合金结构钢钢带按定的螺旋线的角度卷成管坯,然后将管缝焊接来制成,它可以用较窄的带钢 大直径的钢管,主要用于石油、天然气的输送管线。根据管壁厚薄来分,钢带等比较薄的材料制成的管子可以使用高频焊接,有些薄壁管可以用保护气体焊接;壁厚超过mm的管材可以用手弧焊。